In the recent virtual edition, VC highlights successful ventures such as Intera, a manufacturer from recycling; Beeler Craft Brewery and Surroundings Restaurant.
The newspaper La Campana publishes some of the interesting reports contained in the 24th edition of Visión Comfacauca, which can be seen on the website of the Compensation Fund.
Intera protects the environment by giving new life to plastic
Recently graduated in 2006 from industrial engineering at the Popayán University Foundation (FUP), Andrés José Paz Arboleda, worked at the Technological Institute of Comfacauca, today Unicomfacauca, as administrative and financial vice-rector in charge, after a while he stayed at the institution and there began, not only his professional history, but his approach to recycling as a businessman.
At that time, the Mayor’s Office, the Governor’s Office and universities began to think about developing a project in the then El Ojito sanitary landfill, in Popayán, with some equipment that had been resting on that site for a long time.
He got into that open-air dump, where he found recyclers who empirically separated materials, with which they produced shoe soles, which shocked him, because he would not have imagined it.
The project began to be given structure, but in the end the Mayor’s Office, the Governor’s Office and the universities did not agree. Paz Arboleda did not stand still before that shipwreck and took the initiative in a personal capacity. His first approach to the industry was a small factory that produced objects from recycled glass.
That company ended, but not his desire for the transformation of waste materials, because while he saw them as raw material, he also thought about contributing to the environment and generating employment. He decided to give shape to the project aborted by the institutionality and the academy, with the recycling of plastic. He took “infinite affection”, as he puts it, to the harvesting process. At that time there was no thought in this field, no one had any idea of how to transform materials, much less how to do it and what equipment to use.

future business.
He began to investigate recycling, how it worked, in what way, what was happening in Popayán in this regard, in Bogotá and in the world. He realized that Europe and the United States were very focused on recycling, but not in Colombia. He knew that the recycling of metal and paper was well structured, but plastic was not, which is the biggest pollutant on the planet, especially in the seas, rivers and forests.
His persistence and stubbornness have led him to develop recycling engineering and technology.
in a variety of plastic, obviously with hits and misses, but growing in this
industry. He set up the factory in Mosquera, Cundinamarca, and in 2019 moved it to
Popayan. Visión Comfacauca spoke with this industrialist from Payana.
What is the origin of the Intera project?
A.J.P.A. I found out that in the United States and in Europe there were transformation processes
made of plastic, more focused on virgin material, but the collection and
separation of materials. There I begin to give shape and structure to the project, focused
to a plastic extrusion process. He saw that in Cauca the enclosures of pastures and
cattle corrals were made by cutting down the forest to meet the need for infrastructure,
at the expense of water due to deforestation that dries up the sources. So with the help of a
technician, I turned on that old extruder from El Ojito, zero technologies, I put a spell mold on it and
I took out a plastic stringer. At the ITC I requested unpaid leave for a month and
I started to investigate. I ran into a person in Bogotá who knew about extrusion equipment.
I told him what characteristics the model required, he told me that it could not be achieved, I was stubborn and
i made it.
Who accompanied you on that project?
A.J.P.A. In 2009 I associated with my uncle Carlos Felipe Chaux, and in October of that year
I contracted the manufacture of a machine in Bogotá, the first stop was hard, we had to
put more money into the team and after six months we started the line. I have always been
passionate about this topic, if it is not done with passion, nothing is achieved. I have been an operator of my
own production line. It took six months of trial, trial and error, spending a few
resources, until the first product was delivered, we couldn’t believe it. I put it on the market
in July 2010, a year in which we did well. In 2011 we made the decision to buy
teams with better technology, more efficient, with different capacities, thinking of a
future business.
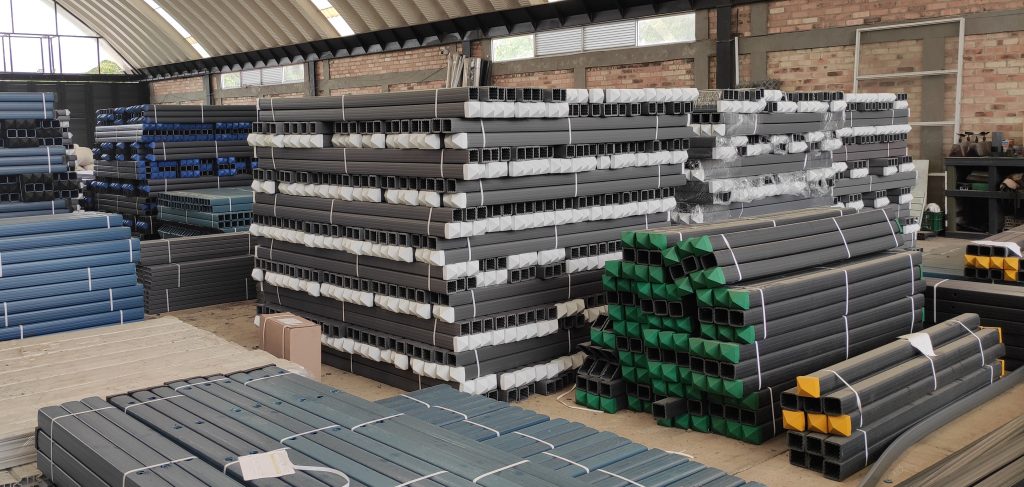
bending is higher than other material.
Where was the factory established?
A.J.P.A. In Mosquera, Cundinamarca, he was there until 2019. Two years earlier, in the
2017 the commercial, operational work began. Starting a business is not easy, in
special from the task of collecting the materials, to make an organized recycling for
produce quality raw material. It’s 12 years of work. Giving formality to recycling has
been a big challenge.
What made you return with the company to Popayán?
A.J.P.A. He lived in the north of Bogotá and the plant was in the municipality of Mosquera, they were
three hours out and three in a day, there were days that were up to five hours in the
mobilization. In 10 years a wear and tear began to take place. The quality of life in Bogota,
It depends on whether work is close to home. In addition, with my partner we saw the possibility of
contribute to Popayán, since many of those who have left the city believe that returning is
going back in time, stagnating, I see it differently, because I also feel that here
there are the opportunities.
What happened with the decision to move to Popayán?
A.J.P.A. They told me that I had gone crazy. At first I was scared, especially
because it had a captive market in the center of the country, especially in Bogota,
Cundinamarca, Magdalena Medio, Santanderes, etc. Staying away from my clients
it was hard.
Did you evaluate the costs to return to Popayán?
A.J.P.A. Of course, that has to be evaluated a lot. Make business assets in Colombia
it’s hard. If we look at the history of the companies in the country, which have raised capital and have
Well-structured companies today are from 50-60-70 years ago because in those times there were
More possibilities, less competition. Today making business assets is very
complex, costs do not allow it, the tax burden is very high, the banks squeeze
strong. Obviously, in Bogota the fixed cost is higher and makes companies fail in
the attempt. That was also one of the reasons why we thought about the transfer.
How many jobs was it generating in Bogotá?
A.J.P.A. Fifteen direct jobs and more than 100 indirect jobs. In Popayán we are generating
32 direct jobs and more than 100 people around recycling, in addition to others in
Different fields.
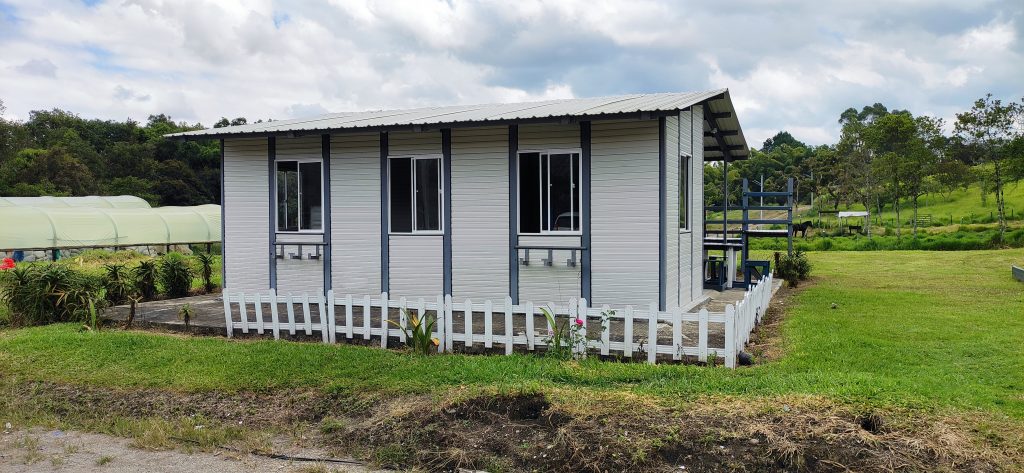
Having just arrived in Popayán, how did Intera do in unemployment, blockade, quarantine and
pandemic?
A.J.P.A. It was very hard, all the staff are linked to the company. on the dole
they were 47 days without being able to enter the plant, almost 80 days without raw material. Then came the
quarantine, with all that confinement implied, the workers remained in the plant,
staying in a house made with the plastic material that Intera produces. With the support of
the partners of the company, all the logistics and resources were available so that they could
stay at the plant, that was the way to get it going. In the pandemic we were
unemployed for about 23 days, longer was the paralysis caused by the strike, which generated
many economic and financial havoc.
Does all type of plastic serve for the industrial transformation that Intera does?
A.J.P.A. There are seven classes of plastics, the PVC industry is different from Polyethylene
Terephthalate, known as PET, in the plant we only use a polypropylene and a
high density polyethylene. We train recyclers in collection, we look for
Improve your quality of life. We have partnered with associations, especially Armac,
with which we have structured a future work, because to think that Intera can be
supply 100% of Popayán, it is not possible. We are doing on average one
transformation of 50 tons per month, in Popayán we mark around 10, 12 or 15
tons maximum, we start at zero, most of it comes from outside.
What disposables does Intera use?
A.J.P.A. The entire line of household cleaning, liquid containers, laundry shampoo,
detergents, cans of car oil, etc. You have to identify them and separate them from the rest of the
recycling.
What products is Intera bringing to the market?
A.J.P.A. We have three product lines. We are focused on solutions
enclosure for rural and urban housing, delimitation of paddocks, lots, etc. the plastic in
these cases is like wood. Tables, benches,
chairs, pots, floors, street furniture, classrooms, warehouses, etc. Plastic as a material
prima is the most durable and aseptic material, its bending capacity is greater than
any other, the resistance and rigidity are excellent. The profiles are worked by
colors and custom